
Case in America:Lithium-ion battery is safer for the forklift drivers base on OSHA estimates
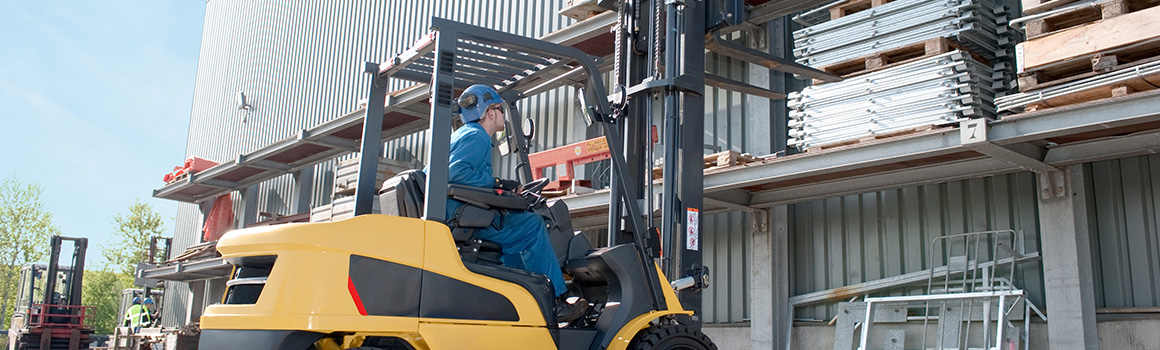
OSHA(The Occupational Safety and Health Administration in USA) estimates that each year, approximately 85 workers are killed in forklift-related accidents. In addition, 34,900 accidents result in serious injury, with another 61,800 classified as non-serious. One of the hazards workers must contend with when operating forklifts is the battery.
New advancements, however, are making forklifts safer to operate, with more companies in the material handling industry investing in lithium-ion technology to power their equipment.
Lithium-ion batteries offer several benefits, including increased efficiency, reduced maintenance, and a boosted cost savings. One of the biggest benefits is their enhanced safety features.
JB BATTERY is a professional forklift lithium-ion battery manufacturer. JB BATTERY LiFePO4 forklift battery is deep cycle lithium battery, it’s high performance and much safter than Lead-Acid battery.

Below, we’ll explore five ways a lithium-ion battery makes your forklift safer to operate so that you can be assured you’re getting the most out of your investment and protecting your employees in the process.
1. They Don’t Require Watering
Because of the way lithium-ion batteries are designed, they do not require watering. Lithium-ion batteries are sealed shut, which require little maintenance to upkeep.
Lead-acid batteries are filled with electrolyte (sulfuric acid and water). This type of battery generates electricity through a chemical reaction of lead plates and sulfuric acid. They require regular refilling with water or the chemical process will degrade and the battery will suffer an early failure.lead-acid-forklift-battery
Watering a battery comes with several safety hazards, and workers must take great care to minimize any risks. This includes only topping off with water after it’s fully charged and cooled down and being careful not to overfill with water.
When the battery is in use, workers must pay careful attention to water levels to account for any water level changes that may occur even after watering the battery is completed.
If a spill does occur, highly-toxic sulfuric acid within the battery can splash or spill onto the body or in the eyes, causing serious injury.
2. There Is Minimal Risk Of Overheating
One of the greatest safety hazards of using lead-acid batteries is overcharging. When this occurs, it can cause the electrolyte solution in a lead-acid battery to overheat. This then causes hydrogen and oxygen gas to form, which increases pressure inside the lead-acid battery.
While the battery is designed to relieve pressure build-up through venting technology, if there is too much gas accumulation, it can cause the water to boil out of the battery. This can destroy the charge plates or the entire battery.
Even more dire, if a lead-acid battery overcharges and then overheats, there may not be a way for the pressure generated from the hydrogen and oxygen gas to relieve itself other than by an instant explosion. In addition to causing severe damage to your facility, an explosion can cause devastating consequences for your employees.
To prevent this, crews must carefully manage and monitor the charging of lead-acid batteries by preventing overcharging, providing adequate fresh air through a ventilation system, and keeping open flames or other sources of ignition away from the charging area.
Due to the Lithium-ion battery structure, they don’t require a dedicated room for charging. One of the best features of a lithium-ion battery is its battery management system (BMS). The BMS tracks cell temperatures to ensure they remain in safe operating ranges so there is no risk to employees.
3. No Separate Charging Station Is Required
As mentioned above, lead-acid batteries require careful monitoring and a separate charging station in order to minimize any risks associated with recharging. If a lead-acid battery overheats when charging, it can cause a build-up of dangerous gases, enhancing the risk of an explosion that can cause worker injury or worse.Lead-acid-chraging
Therefore, a separate space that has adequate ventilation and measures gas levels is necessary so that crews can be notified in time should hydrogen and oxygen gas levels become unsafe.
If lead-acid batteries are not charged in a safe charging room with proper precautions in place, crews likely will not notice unseen, odorless pockets of gases that can quickly become flammable, especially if exposed to an ignition source – something more likely in an unprotected space.
A separate station or room that is needed for the proper charging of lead-acid batteries is not necessary when using lithium-ion batteries. That’s because lithium-ion batteries do not emit potentially harmful gases when charging, so crews can plug lithium-ion batteries directly into a charger while the batteries remain inside the forklifts.
4. Forklift Injury Risks Are Minimized
Because lead-acid batteries must be removed in order to be charged, this must happen several times throughout the day, especially if you own multiple forklifts or operate over the course of multiple shifts.
That’s because lead-acid batteries only last approximately 6 hours before they must be charged. They then require about 8 hours to charge and a cool down period afterward. That means each lead-acid battery only will power a forklift for less than one shift.
Battery swapping in itself can be a dangerous act because of the weight of the battery and the use of equipment to move them. Batteries can weigh as much as 4,000 pounds, and material handling equipment typically is used to lift and swap the batteries.
According to OSHA, the top causes of fatal forklift accidents involve workers getting crushed by tipping vehicles or between the vehicle and a surface. Using material handling equipment each time to remove, transport and reinstall a lead-acid battery after charging increases the risk of an accident for workers responsible for managing the forklift batteries.
Lithium-ion batteries, on the other hand, can remain in the vehicle while connected to a charger. They also can be opportunity charged, and typically have longer run times at 7 to 8 hours before requiring a charge.
5. Ergonomic Risks Are Minimized
Though most forklift batteries require material handling equipment for removal because of their substantial weight, some smaller forklift batteries can be removed by crews. In general, lithium-ion batteries typically weigh less than a standard lead-acid battery.
The lower the weight of the battery, the lower the ergonomic risks among workers. No matter the weight, correct lifting and handling is essential to maximizing safety. This includes positioning your body as close as possible to the battery before moving it, and bending your knees slightly before lifting or lowering a battery.
It’s also important to get assistance from a co-worker, and if the battery is too heavy, use a lifting device. Not doing so can cause neck and back injuries that can put an employee out of commission for an extended period of time.
Final Thoughts
Lithium-ion batteries offer many benefits for companies that want to increase efficiency and improve workflow. For companies that prioritize safety in their operations, lithium-ion batteries are especially valuable thanks to their design, which promotes features such as temperature control, simple charging and a lack of watering requirements. So it’s time to upgrade the Lead-Acid battery to Lithium-ion battery for your forklift.