
Fewer Required Batteries / Maintenance Free
What is the correct battery voltage for your electric forklift?
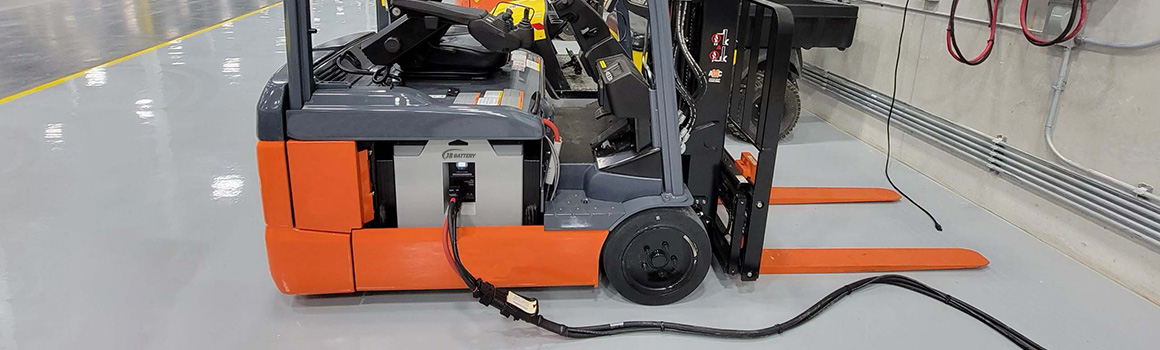
Electric forklift trucks have become increasingly popular in recent years. They are being used mostly in warehouses. The electric forklift is cleaner, quieter and more maintenance friendly than a forklift with a combustion engine. However an electric forklift does require charging on a regular basis. This is no problem for an 8-hour working day. After working hours, you can easily charge the forklift at the charging station. Electric forklifts are available with various battery voltages. What battery voltage does your forklift need?
There are plenty of companies offering industrial batteries for forklifts. Aside from checking the voltage, how are you supposed to know which will be most suitable for your forklift operations?
For what seems to be a simple decision, there’s a surprising level of specificity depending on your precise requirements. Between the pros and cons of lead-acid vs. lithium-ion batteries, cost vs. capacity, different charging systems, and the slight variations between brands, there are a lot of important factors to consider.
Forklift Battery Voltage
Electric forklifts come in a range of sizes and lifting capacities, based on the specific material handling tasks they’re designed for. Unsurprisingly, their batteries also vary significantly due to differences in customers’ energy requirements.
Pallet trucks and small three-wheeled forklifts tend to use a 24-volt battery (12 cells). They’re relatively lightweight machines that don’t need to move particularly fast or lift heavy loads, so these smaller batteries provide plenty of motive power.
A more typical warehouse-type forklift with lifting capacities from 3000-5000lbs will generally use either a 36 volt or 48-volt battery, depending on the maximum driving speed required and how often loads toward the heavier end of the range are to be lifted.
Meanwhile, heavy-duty forklifts aimed more at the construction industry will use a minimum of 80 volts, with many requiring a 96-volt battery and the very largest heavy industrial lifts going all the way up to 120 volts (60 cells).
If you want to calculate the voltage of a battery quickly and easily (where the stickers or other markings are obscured), simply multiply the number of cells by two. Each cell produces approximately 2V, although peak output can be higher when freshly charged.
Voltage and applications
Different usage of a forklift will require batteries with different voltages. A few examples below:
24 volt battery: warehouse trucks (pallet trucks and stackers), plus the small 3-wheel forklifts
48 volt battery: forklift trucks from 1.6t to 2.5t and reach trucks
Battery of 80 volts: forklifts from 2.5t to 7.0t
96-volt battery: heavy-duty electric trucks (120 volts for very large lift trucks)
Voltage and Capacity
It’s vital to make sure the battery for your forklift provides the correct voltage. Some forklift models can be run on a range, depending on operational parameters (usually either 36 or 48 volts), but most are designed to accept batteries with one specific power rating. Check the forklift data plate or the relevant manual for your make, model, and year. Using a forklift with an underpowered battery will affect performance and may prevent operation altogether, whereas too powerful a battery can damage the drive motor and other key components.
The capacity of a forklift battery, usually measured in Amp-hours (Ah), relates to how long the battery is able to sustain a given current. The higher the battery capacity, the longer you can run your forklift (or other electric material handling equipment) on a single charge. The normal range for forklift batteries starts at around 100Ah and goes up to over 1000Ah. as long as your battery has the correct voltage and will physically fit into the battery compartment, the higher the capacity the better.
Charging Time
The downtime your equipment has to spend on charge between uses impacts productivity. Ideally, you want a forklift battery that runs for as long as possible on a single charge but spends as little time as possible at the charging station. This is mostly relevant if you are running a 24-hour operation with operators on shifts. If your site or warehouse is only open during office hours, there’s plenty of time to charge your lift batteries overnight.
The charging time for a forklift battery is a function of the battery charger used as well as the battery 3itself. Different chargers can be single or three-phase and have different charging rates (in Ah). Some also have a “fast-charge” option.
However, it’s not so simple as “the faster the better”. Using a charger that doesn’t match the recommended rate for the battery contributes to sulfation and battery degradation, especially in lead-acid batteries. This ends up costing you significantly, both for battery maintenance and by replacing the battery sooner than if you’d used an appropriate charger.
Lithium-ion batteries tend to have much faster charging times overall and are the better option if fast turnarounds between shifts are required. The other advantage here is many lead-acid batteries require a “cooling off” period after charging. Typically, even with a good brand of charger, a lead-acid battery will require 8 hours for a full charge, and another 8 for cooldown. This means they spend a lot of time out of operation and a customer choosing this type for commercial operations with regular forklift usage may need to purchase several batteries for each lift and rotate them.
Maintenance and Service Life
Most lead-acid forklift batteries for need regular maintenance, and specifically “watering” (the topping up of the electrolyte fluid to avoid undue damage to the electrode plates). This extra task takes time out of their operating schedule and must be dedicated to a suitably trained staff member.
For this reason, some commercial battery manufacturers offer one or more types of maintenance-free batteries. The downsides of these are they are either significantly more expensive than standard wet-cell sort or have a much shorter service life. A typical lead-acid battery will last approximately 1500+ charging cycles, whereas a sealed, gel-filled battery may only be good for around 700. AGM batteries often last even less.
Lithium-ion batteries also generally withstand more charging cycles than their lead-acid counterparts (around 2000-3000). In addition, their greater capacity is such that those from a quality brand will often support running a forklift for two whole shifts per charge. This means their effective service life tends to be even longer in real terms, whilst keeping your electric forklift running without interruptions for battery maintenance.
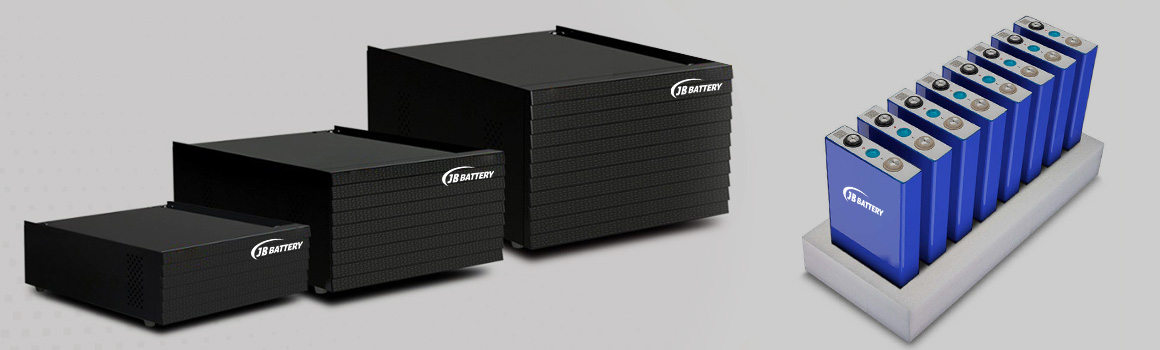
The 6 Types of Forklift Batteries
1. Lead-Acid Forklift Batteries
Lead-acid batteries are the traditional standard technology for industrial battery solutions.
Each cell within the battery consists of alternating plates of lead dioxide and porous lead, submerged in an acidic electrolyte solution which causes an imbalance of electrons between the two plate types. This imbalance is what creates the voltage.
Maintenance and Watering
During operation, some of the water in the electrolyte is lost as oxygen and hydrogen gases. This means lead-acid batteries need to be checked at least once per 5 charging cycles (or weekly for most electric forklift operations) and the cells topped up with water to ensure the plates are fully covered. If this “watering” process is not carried out regularly, sulfates build up on exposed areas of the plates, resulting in a permanent reduction in capacity and output.
There are several types of watering systems available, depending on the battery design. Some of the best watering systems also have automatic shut-off valves to prevent accidental overfilling. Although perhaps tempting as a time-saving measure, it’s very important never to water the cells whilst attached to the battery charger, as this can be highly dangerous.
Charging
If you’re using electric forklifts for commercial material handling applications, a significant downside to this type of battery technology is the amount of downtime dedicated to charging.
Approximately 8 hours for a full charge, plus the time taken for the battery to cool as they get very hot during charging, means most of a day out of action.
If your equipment is in heavy use, you’ll need to purchase several batteries and swap them in and out for charging.
It is also unwise to perform “opportunistic” charging on lead-acid batteries i.e. charging them when convenient even if not depleted to at least around 40%. This causes damage which reduces the service life considerably.
2. Tubular Plate, AGM, and Gel-filled Batteries
In addition to the standard, flooded, flat-plate lead-acid batteries described above, there are several variations that produce electricity in a similar way but applying advanced technology to make a product potentially more suitable as a forklift battery.
A tubular plate battery is a system where the plate materials are combined and held within a tubular structure. This enables fast charging and reduces water loss, meaning less maintenance and longer service life.
Absorbed Glass Mat (AGM) batteries use mats between the plates which reabsorb oxygen and hydrogen. This results in a significant reduction in moisture loss and maintenance requirements. However, these are very expensive compared to other options.
Gel batteries use a similar electrolyte to flooded wet-cell batteries, but this is turned into a gel and placed in sealed cells (with a vent valve). These are sometimes called maintenance-free batteries because they do not need to be topped up. However, they still lose moisture over time and have a shorter service life than other lead-acid batteries as a result.
Flat-plate lead-acid forklift batteries will last around 3 years (around 1500 charging cycles) if cared for properly, whereas their albeit more expensive tubular-plate counterparts will keep going for 4-5 years under similar conditions.
3. Lithium-ion Forklift Batteries
The emergence of lithium-ion batteries, first developed in the late 1970s, provided a maintenance-free commercial alternative to lead-acid systems. A lithium-ion cell contains two lithium electrodes (an anode and a cathode) in an electrolyte, along with a “separator” preventing unwanted ion transfer within the cell. The end result is a sealed system that doesn’t lose electrolyte fluid or require regular topping-up. Other advantages over traditional lead-acid batteries for material handling equipment include a higher capacity, faster charging times, longer service life, and reduced operator hazard as there are no unsealed chemical components.
Lithium-ion forklift batteries are more energy-efficient and charge faster than lead-acid batteries, saving you time, and so saving money.
Lithium-ion batteries don’t need to be swapped out and can be opportunity-charged during operator breaks.
Lithium-ion forklift batteries don’t require traditional maintenance like watering or equalizing.
Lithium-ion forklift batteries don’t require traditional maintenance like watering or equalizing.
Operators can enjoy longer run-times and zero decline in performance as the battery discharges with forklifts powered by lithium-ion batteries.
Lithium-ion batteries have no emissions and their longevity may mean less battery disposal in the future.
Businesses can reclaim the area being using as a charging room for additional storage.
Overall, lithium-ion batteries are generally considered superior to most types of lead-acid batteries as long as the purchase price isn’t prohibitive and you are able to compensate for the reduction in weight.
JB BATTERY high performance LiFePO4 packs
We offer offer high performance LiFePO4 battery packs for manufacturing new forklifts or upgrading used forklifts, LiFePO4 batteries contain:
12 volt forklift battery,
24 volt forklift battery,
36 volt forklift battery,
48 volt forklift battery,
60 volt forklift battery,
72 volt forklift battery,
82 volt forklift battery,
96 volt forklift battery,
customized voltage battery.
Our LiFePO4 bttery packs’ advantage: constant power, faster charging, reduce downtime, fewer required batteries, maintenance free, it’s particularly suited for forklift.